Sweaters constructed from unused stockings, carpets stitched from scrapped T-shirts, handbags woven from grass, and textile factories actually implementing green, ethical and transparent work standards. These are important phenomena because textiles are more than just clothes and fashion. They are part of something much bigger -- social movements, ecological concerns, cultural evolution, industrial responsibility and even politics.
With this in mind, Goethe-Institut held their annual Hamburg symposium, "Green Cycles -- Corporate Social Responsibility in the Textile Cycles", for the very first time in Bangkok last month. The event, organised by Marla Stukenberg, director of Goethe-Institute Thailand, is part of IKAT/eCUT, a two-year-long project that explores the function of textiles in Asia Pacific from different perspectives.
The symposium in Bangkok featured German and Thai experts, and academics sharing knowledge, information and current achievements on sustainable textiles to increase public awareness on the shift the textiles industry may be about to undergo, and that it should make in the future. Much of the discussion revolved around the antithesis of "fast-fashion" -- cheap products, fast turnover and questionable ecological and ethical standards -- and instead put emphasis on the concept and practice of "sustainable fashion", an idea that's taking off in Thailand and other parts of Asia.
We talk to two Thai speakers featured from the symposium trying to make sustainable textiles a mainstream reality.
Sustainable capitalism
Jarupatcha Achavasmit, a textile designer, lecturer at King Mongkut's Institute of Technology Ladkrabang and design consultant for multiple textile foundations, is looking to do the seemingly impossible: make Thai crafts and fabrics relevant in contemporary society.
"When talking about sustainability, most people focus on the material and environmental side of it. How do we upcycle, recycle, reuse and remake?" she says on the phone a few days after her presentation. "But what I've been interested in since I was studying in the US and UK is social sustainability. How do we maintain cultural identity and knowledge in order to expand, or revive it to become more relevant?"
For the past three years, Jarupatcha has been working with the Chaipattana Foundation to develop and design projects in order to create accessory products from vetiver grass -- ya faak, an extremely sustainable plant that not only needs a little water and no pesticides and fertiliser to grow, but also protects the land from natural disasters. The project met with so much success that Her Royal Highness Princess Maha Chakri Sirindhorn requested that she lead more projects with more local materials such as reed (or kok, used for making Thai traditional mattresses), silk and cotton.
A textile designer who can weave all sorts of materials, from silk to stainless steel, Jarupatcha's love of textiles started at just three years old, when she first learned how to sew from her seamstress grandmother. She studied industrial design at King Mongkut's Institute of Technology Ladkrabang, before receiving a scholarship to the University of Michigan, Ann Arbor, which is where she determined her mission would be social sustainability in Thailand.
"I had an amazing weaving tutor named Professor Sherri Smith. It was she who suggested I study Thai textiles and see how I can make them contemporary."
Jarupatcha continued this quest at Central Saint Martins in London, conducting research on sustainable textiles, and what she discovered was a simple solution that may startle many nature-loving minds.
"I learned that you have to work with capitalism," she explains. "You can't go against it. Traditional knowledge, especially with textiles, in a way is a commodity. One way to make it continue is you have to put economic value into it so people earn a living. So when they gain confidence that they can earn a living from making crafts, it'll encourage them to continue. Then it would encourage the younger generations to continue the knowledge."
For her vetiver grass project with Chaipattana foundation, Jarupatcha took her students to Kokprong, Phetchabun, to learn the skills and local knowledge surrounding the material. Combining everything they learned, the students designed prototypes that the local craftsmen would then make.
"Each student designed a collection, but it had to fit the market needs, as we aimed to sell abroad as well. In the end we had 21 beautiful vetiver collections, both in fashion and home decor. It's still local knowledge, but we make it in a way that contemporary society can use and like."
But with Thais being so brand-obsessed, getting people to buy it is a challenge in itself. In order to sell to the Asian market, Jarupatcha says that organisations have to establish themselves as brands.
"We have to make what they love and they will love us," she says. "I never blame the consumers, as they act naturally. I blame myself that we can't make something good enough for the consumers to love and value.
"There's a very strong sense of individualism in Europeans. When they consume things, they don't care about fashion or what others think. For Asians, it's a different culture. They need reassurance, first, from the people around us that the brand is good, and then we will consume it. So this can be a healthy perspective, because if a Thai brand can create assurance, then people will flock to buy its products. Small brands can spring up very fast with consumers who follow each other and move in masses. I'm optimistic about it. My idea is also part of the sustainable movement, which focuses on social and economic sustainability as well as the environmental impact of things."
-- Apipar Norapoompipat
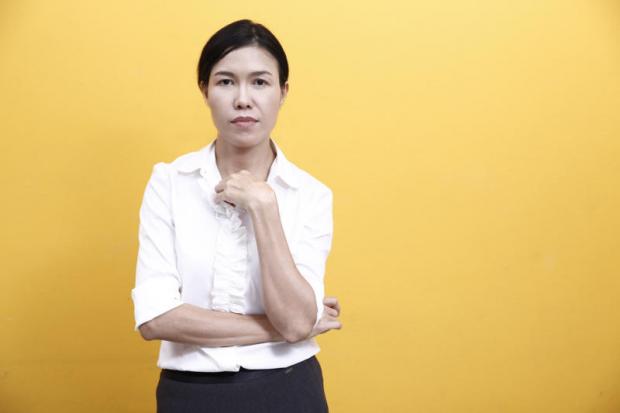
Roongtip Luilao.
Scrap happy
Deeply involved in the design business, Roongtip Luilao realised it was her responsibility to take care of the environment, because designers are among the chief culprits creating waste from production. Scrap Shop and Scrap Lab were founded to prove the design industry can be environmentally-friendly as well.
Scrap Shop describes itself as an "eco-venture". It was launched in 2010 at Kasetsart University's Faculty of Architecture, and the idea is to promote products crafted from reusable waste materials. Scrap Shop is the retail end of the Creative Centre for Eco-Design, or Scrap Lab, which conducts research and works with designers on how to develop discarded materials into functional products. Scrap Shop offers a range of goods, not only textile and fabric-based items but furniture (sofas made out of old banker uniforms) and wooden toys.
"For me, products considered sustainable should be made out of materials that enable use over and over again. Resources used in their production should already exist," says Roongtip, home-economics lecturer and consultant to Scrap Shop and Scrap Lab.
Scrap Lab explores different kinds of waste from both industrial and individual consumers. Once waste comes in, they research and consult with professionals from fields such as science and engineering to develop scrap or waste into raw materials that can be converted into new products. "We implement the upcycling concept with the waste we have," says Roongtip. It's the process of transforming by-products and waste into new materials or products that have better quality and better environmental value."
According to Roongtip, two main causes of industrial waste are machines' incapacity to work on small-piece materials and slacker employees who make no attempt to use smaller materials.
"If possible, we always suggest they use scrap first, but, at the end of the day, if scraps still remain, manufacturers should exploit them in a new business. This is called circular economy, with one industry providing materials to another industry," Roongtip says.
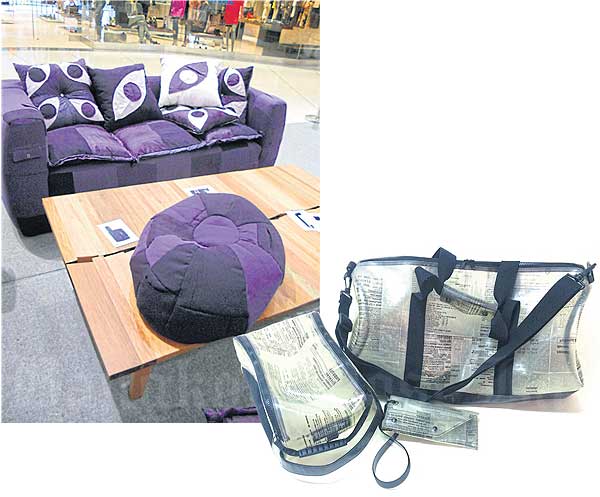
A successful case of circular economy that Roongtip and her team have been working on includes using scraps from a jeans-making factory to make new denim sheets, a material for coffee-table covers. Another case is coconut spathes left from the extracting of coconut oil, which have been developed into composite materials to create packaging.
It's been eight years since Roongtip worked with scraps, and some changes have begun to occur in the business.
"From the consumer side, they now believe in our products -- that they're safe to use, unlike in the old days, when they might not feel comfortable with using something made out of waste," explains Roongtip. "For designers, back then not many enjoyed working with scrap, as it was hard. But now they know that it's possible to do so, and it also challenges their creativity. Though environmental concerns are not everyone's primary objective, it of course does help the whole industry."
Asked if it's possible for the Thai design industry to achieve sustainability, Roongtip is hopeful. "If we give enough importance to developing knowledge benefiting the industry, it can definitely happen. We can begin developing from what we have, like raw materials from waste, and integrate it with local wisdom or even technology like 3D printing. This way, the whole business can be a lot more interesting while ensuring sustainability."
-- Pattramon Sukprasert