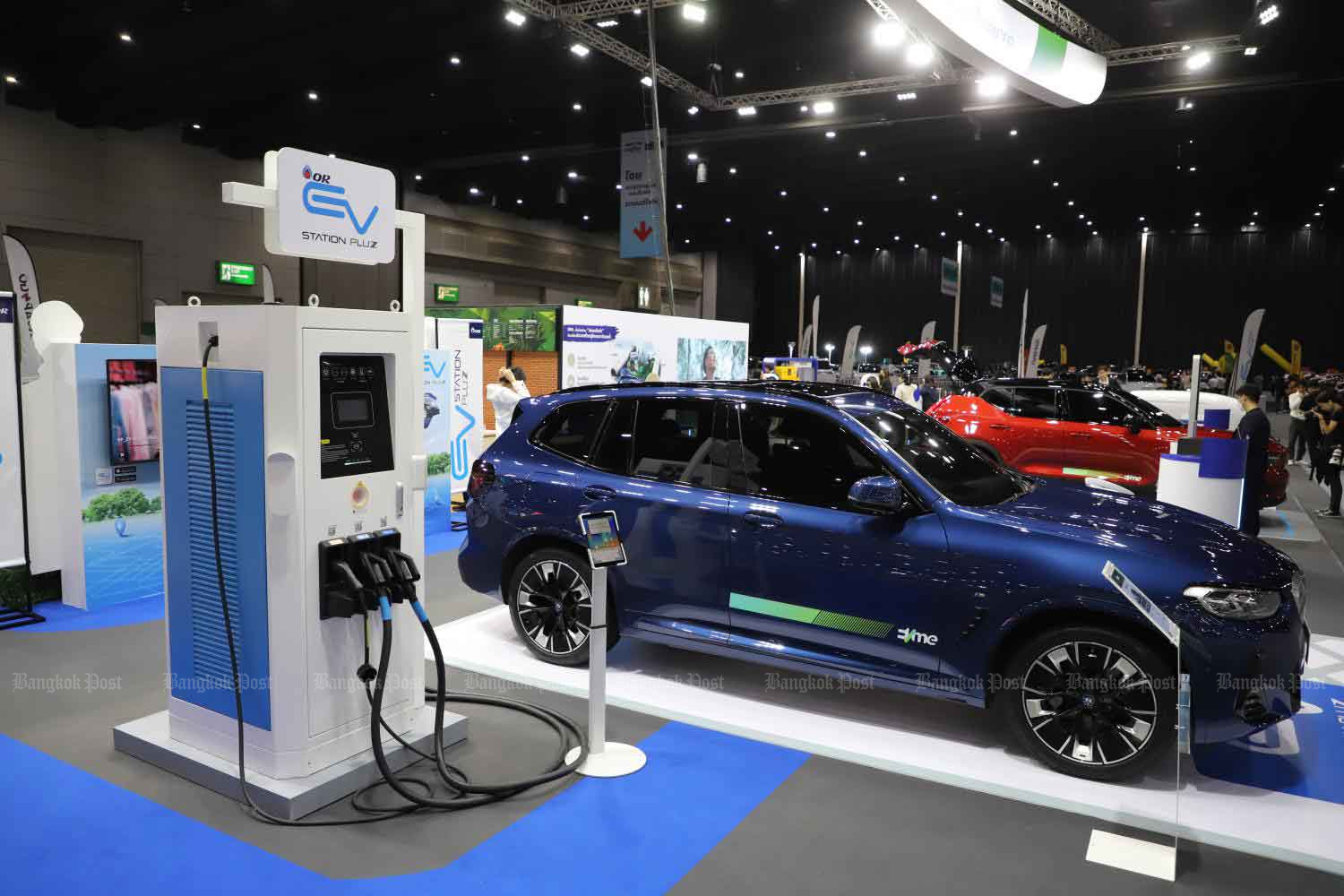
The rapid growth in electric vehicle investment in Thailand from many Chinese EV makers is, in the eyes of some industry observers, reminiscent of "zero dollar" tours.
In this tour scam, which made headlines in 2016, Chinese visitors were lured into buying cheap tour packages in Thailand, but were forced to buy unusually expensive souvenirs and services during their stay.
Only Chinese tour operators and shop owners in their network rake up money, with little or no benefits for the Thai tourism industry.
Saroge Vasuvanich, honorary vice-president of auto parts maker Thai Summit Group Plc, said Chinese EV investment reminded him of zero dollar tours because the companies not only manufacture EVs, but also bring in producers of EV components to build an EV supply chain in the country.
Similar to zero dollar tours, the Chinese firms do not buy products from Thai companies, according to a media report citing Mr Saroge, also a member of the executive board of the Federation of Thai Industries (FTI).
Other business leaders are aware of the impact of the EV industry on Thai manufacturers specialising in parts for internal combustion engine (ICE) cars, but they do not believe the Chinese EV supply chain will develop in the same manner as zero dollar tours.
ZERO KNOWLEDGE
The arrival of Chinese producers of EV components, including batteries, is important to serve the fledging industry when local auto parts makers have little or no knowledge of electric mobility technology, said the Thai Automotive Industry Association (TAIA).
The establishment of the Chinese EV supply chain could be viewed negatively, but the association sees it differently, said Suwat Supakandechakul, president of the TAIA.
He said Thailand needs to be open-minded about investors' plans to run EV-related businesses in the early stages of industry development as local parts manufacturers, steeped in ICE technology for decades, cannot make and supply EV components for assemblers.
"We have to accept that EV technology is new in Thailand and the government needs to draw foreign investors, mostly Chinese, specialising in the technology to jointly build an EV infrastructure," said Mr Suwat.
The FTI's Automotive Industry Club acknowledged the shift is sparking concern over disruption in ICE-related businesses, but it believes the situation will improve in the long term.
In the future, when Thai companies fully grasp EV-related technology, there should be clearer business opportunities as Chinese EV makers are expected to consider outsourcing, similar to how other automakers in the ICE segment from Japan, Europe and the US behaved, said Vithavat Thongves, secretary-general of the club.
Local EV maker Horizon Plus, a joint venture between PTT Plc's wholly-owned Arun Plus and Taiwan-based Hon Hai Precision Industry Co, a multinational electronics manufacturer, concurred with this sentiment.
"We are in the early stages of the EV market, so it is not easy to analyse whether the 'zero dollar tour' phenomenon will happen in this segment," said Buranin Rattanasombat, PTT's chief new business and infrastructure officer and chairman of Horizon Plus.
He noted the development trend of the Thai automotive industry, as Japanese car companies expanded their production facilities here 30-40 years ago to reduce labour costs. Later they partnered with local businesses, which became a key factor in making Thailand a major car production base, said Mr Buranin.
The country has the potential to produce up to 2 million cars a year, he said.
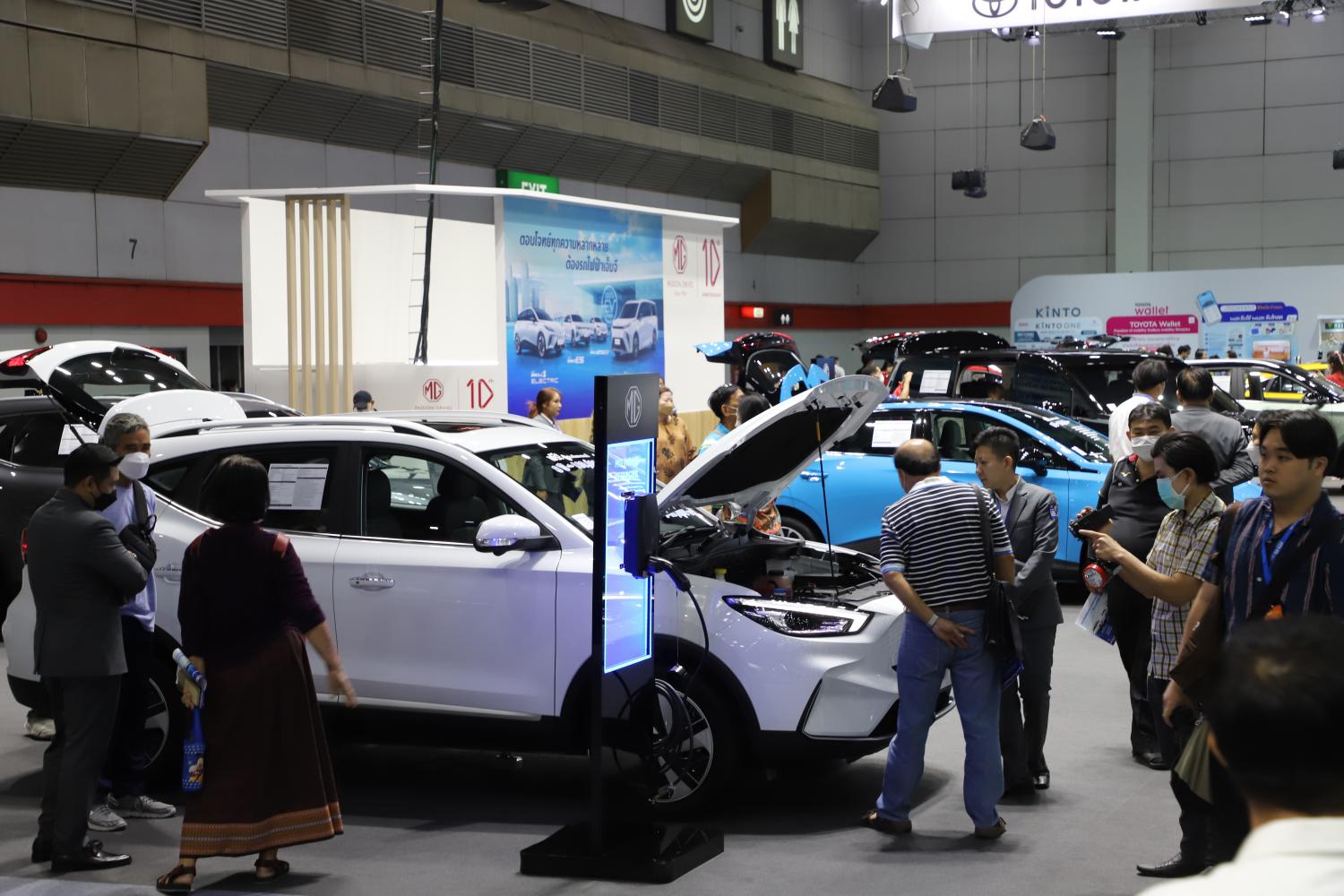
Visitors examine electric vehicles at the Motor Expo 2023. Wichan Charoenkiatpakul
BUSINESS ARENA
Addressing the nature of EV businesses, Amorn Sapthaweekul, deputy chief executive of Energy Absolute Plc (EA), said it is not a surprise to see local auto parts firms struggle to survive in the increasingly competitive EV market following the arrival of Chinese EV component makers.
"This is normal in business competition," he said.
EV assemblers need to partner with reliable parts suppliers and manufacturers who can offer quality products at competitive prices, as well as good after-sales services, said Mr Amorn.
"As a pioneer in the Thai EV industry, our company also seeks to cooperate with suitable partners," he said.
EA, a renewable energy and EV developer and operator, is not restricted to buying EV components from certain countries, acquiring materials from Southeast Asia and China.
The company operates a factory to make commercial EVs in Chachoengsao and produces batteries for EVs in the same province.
EA partnered with a key Taiwanese battery producer, Amita Technologies, in 2017. EA also invested in the Taiwanese firm and has become a major shareholder.
The company spent 6 billion baht building a lithium-ion battery factory that started operation in 2021. Its production capacity is 1 gigawatt-hour per year in the first phase, expected to increase to serve the growing EV industry in Thailand.
SAVING LOCALS
The industry's growth, driven by a shift towards more environmentally friendly cars, is causing both the state and private sectors to help local auto parts makers gain access to the EV supply chain.
Government agencies, including the Board of Investment (BoI), as well as the FTI are urging car companies to use certain EV components manufactured domestically, as well as transfer technology know-how to auto parts makers.
EV manufacturers participating in the state's EV3.0 and EV3.5 incentive schemes are committed to use certain products made in the country, including battery management systems, drive control units, reduction gears and air conditioning compressors, said Narit Therdsteerasukdi, secretary-general of the BoI.
EV3.0, launched during the Prayut Chan-o-cha administration, includes tax cuts and subsidies aiming to promote EV consumption and production between 2022 and 2023.
Participating companies are required to produce EVs in Thailand starting from 2024.
The EV3.5 incentive package also includes subsidies as well as reduced import duties and excise tax. Participants of this scheme, running from 2024 to 2027, must start producing a domestic version of EVs from 2026.
The BoI also requires EV manufacturers taking advantage of its promotions to buy certain EV parts produced domestically, while helping their business partners, who are local auto parts makers, get the hang of electric mobility technology, said Mr Narit.
This should pave the way for local producers to become suppliers of EV components in the future, he said.
The BoI has granted tax incentives to 103 projects worth 77.1 billion baht in EV-related segments. The projects include EV assembly, battery manufacturing and EV charging stations.
The agency also organises activities to help local auto parts makers seek new business opportunities, including business matching events between EV companies and auto parts manufacturers.
Last year, the BoI cooperated with global EV companies from China and Europe to jointly launch the Sourcing Day campaign to promote EV components produced in the country.
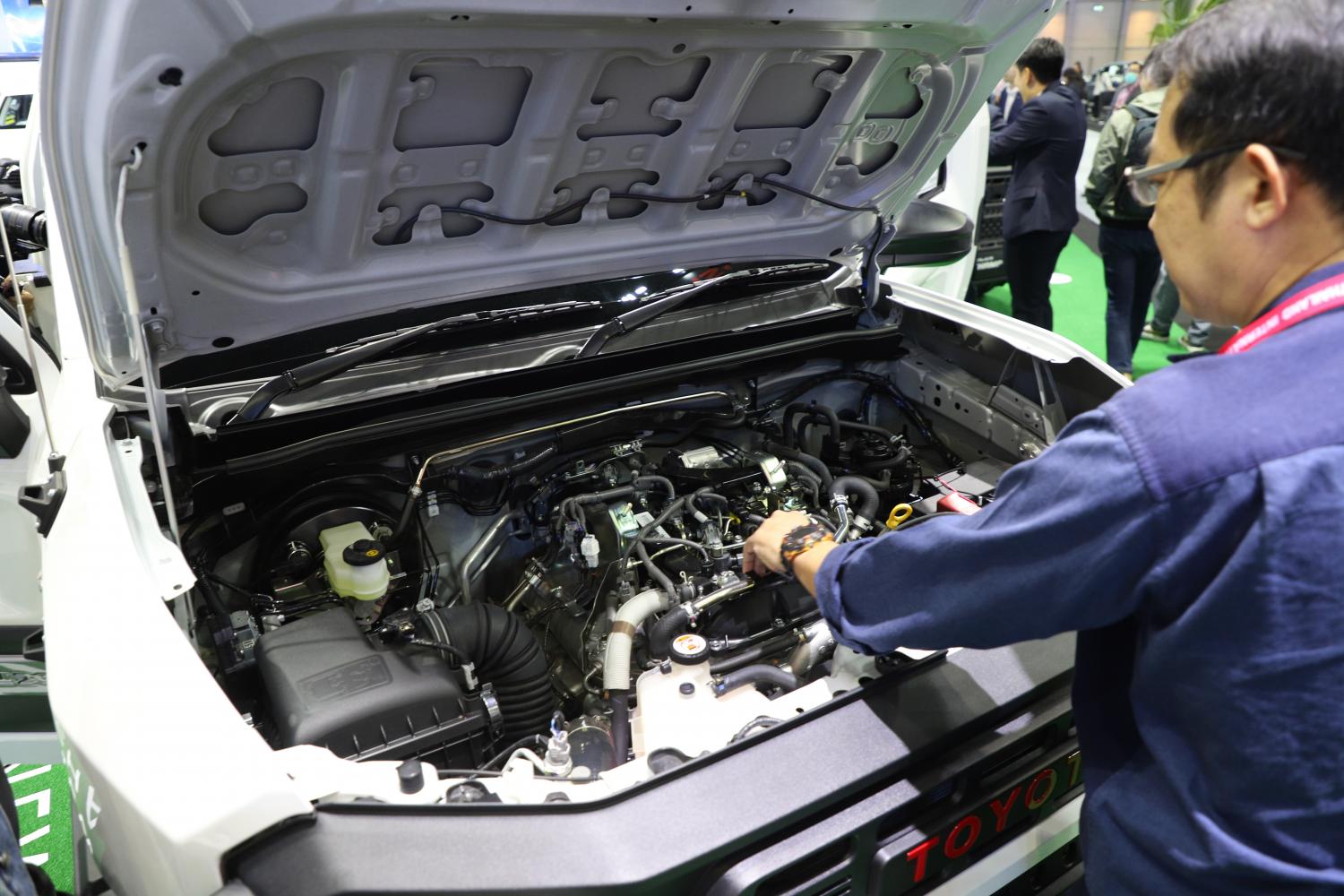
A visitor looks under the hood at an EV at Motor Expo 2023. Pattarapong Chatpattarasill
TECH TRANSFER
Meanwhile, the FTI is collaborating with EV makers, including Chinese companies, to help local auto parts makers with EV technology transfer under a project to develop EV-related businesses, overseen by the Cluster of FTI Future Mobility-ONE.
"We are working with various brands to equip auto parts manufacturers from tiers 1 to 3, as well as students with EV know-how," said Mr Vithavat.
According to the FTI, most of the 1,700 auto parts makers in Thailand are small and medium-sized original equipment manufacturers, categorised as tier 2 and tier 3.
Auto parts producers in tier 1 are usually subsidiaries of global car companies.
These 1,700 companies supply 1.9-2 million components to ICE car manufacturers.
Up to 70% of the auto parts are needed for the production of pickups, while the remaining 30% are used for passenger cars, said the FTI.
Budget is a key constraint for auto parts companies as the shift from ICE to EV technology is costly, said Anujtha Jaovisidha, secretary-general of the Thai Auto-Parts Manufacturers Association.
"We are helping these companies by introducing them to EV technology and financial resources," she said.
"Cooperation with car companies, academic institutions and the BoI is needed to improve their capabilities."
The association has 600 members, mostly in tier 2 and 3.