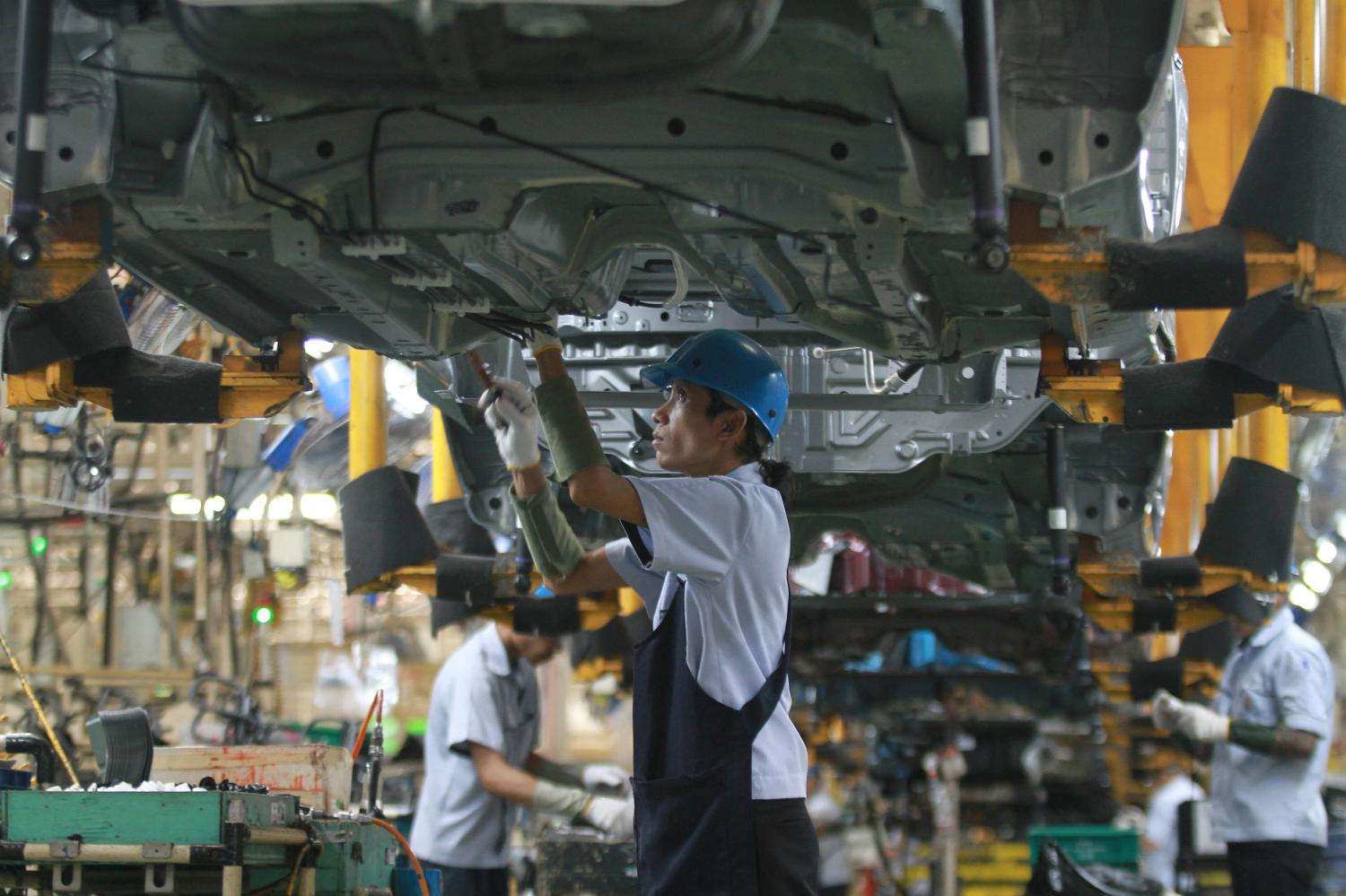
Recent decisions by two Japanese automakers to close their plants in Thailand affect the country's standing as a leading global car producer, once dubbed the "Detroit of Asia".
The announcements by Subaru and Suzuki Motor Corp to cease operations at their car assembly facilities by the end of 2024 and 2025, respectively, follows the closure of 1,600-1,700 factories in several industries, as reported by the Federation of Thai Industries (FTI).
The shutdowns prompted a critical examination of the industrial sector, which is grappling with the transition to modern manufacturing from industries dominated by outdated technologies such as internal combustion engines (ICE) and hard disk drives, often referred to as the "old world".
Entrepreneurs and economists are calling on the government and business sectors to eliminate obstacles to industrial development, increasing the number of skilled workers in high-tech fields and enhancing the country's competitiveness amid rapidly evolving technologies.
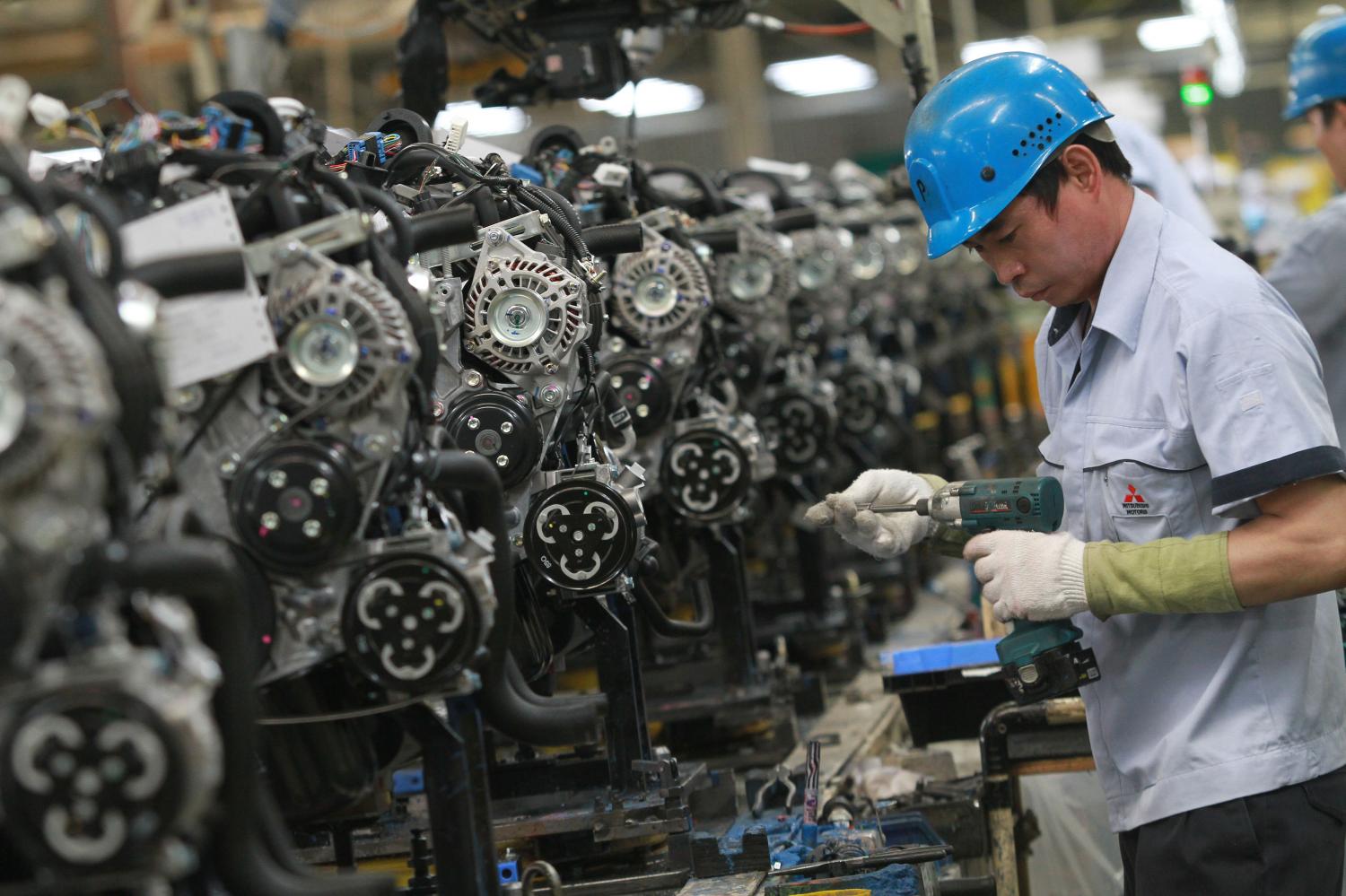
A worker prepares to use a drill on a production line at a car plant in Laem Chabang Industrial Estate. Somchai Poomlard
DETROIT OF ASIA
The government's push to develop the electric vehicle (EV) industry may help Thailand retain its Detroit of Asia moniker, but uncertainties remain as the country faces a shortage of EV experts and workers. Manufacturers are seeking the most suitable countries for their EV investments, with regional neighbours emerging as major car manufacturing rivals.
"Detroit of Asia will be with us because of the state's EV investment promotion," said Surapong Paisitpatanapong, vice-chairman of the FTI and spokesman for the federation's Automotive Industry Club.
EV manufacturing is one of the 12 targeted S-curve industries to be developed within the Eastern Economic Corridor (EEC), covering parts of Chon Buri, Rayong and Chachoengsao. The EEC is projected to become the country's high-tech industrial hub.
The 12 industries comprise: new-generation cars (EVs); smart electronics; affluent, medical and wellness tourism; agriculture and biotechnology; food; robotics for industry; logistics and aviation; biofuels and biochemicals; digital; medical services; defence; and education development.
Authorities launched EV incentive packages, encouraging car companies to invest in Thailand, with Chinese EV manufacturers commanding a significant share of EV investment.
"We welcome investment in battery EVs, plug-in hybrid EVs and hybrid EVs," said Mr Surapong.
The government set a goal for battery EVs to comprise 30% of total car manufacturing by 2030, including the production of 725,000 zero-emission cars, 675,000 electric motorcycles and 34,000 electric buses and trucks.
He acknowledged domestic car sales in Thailand have decelerated as banks impose stricter auto lending criteria amid ballooning household debt, but this was not the main reason that led Suzuki to close its factory in Rayong next year.
In a statement released on June 7, the Shizuoka-based car manufacturer said it aims to focus resources on producing electric and hybrid cars elsewhere.
The decision is part of Suzuki's plan to adjust its car production strategy worldwide. The company will import vehicles, including EVs and hybrids, from plants in India and Indonesia, for example, said Mr Surapong.
"India and Indonesia have larger populations than Thailand. I believe Suzuki also looked for countries with lower production costs than Thailand," he said.
"We have more expensive electricity bills and wages than those two nations, as well as a smaller market."
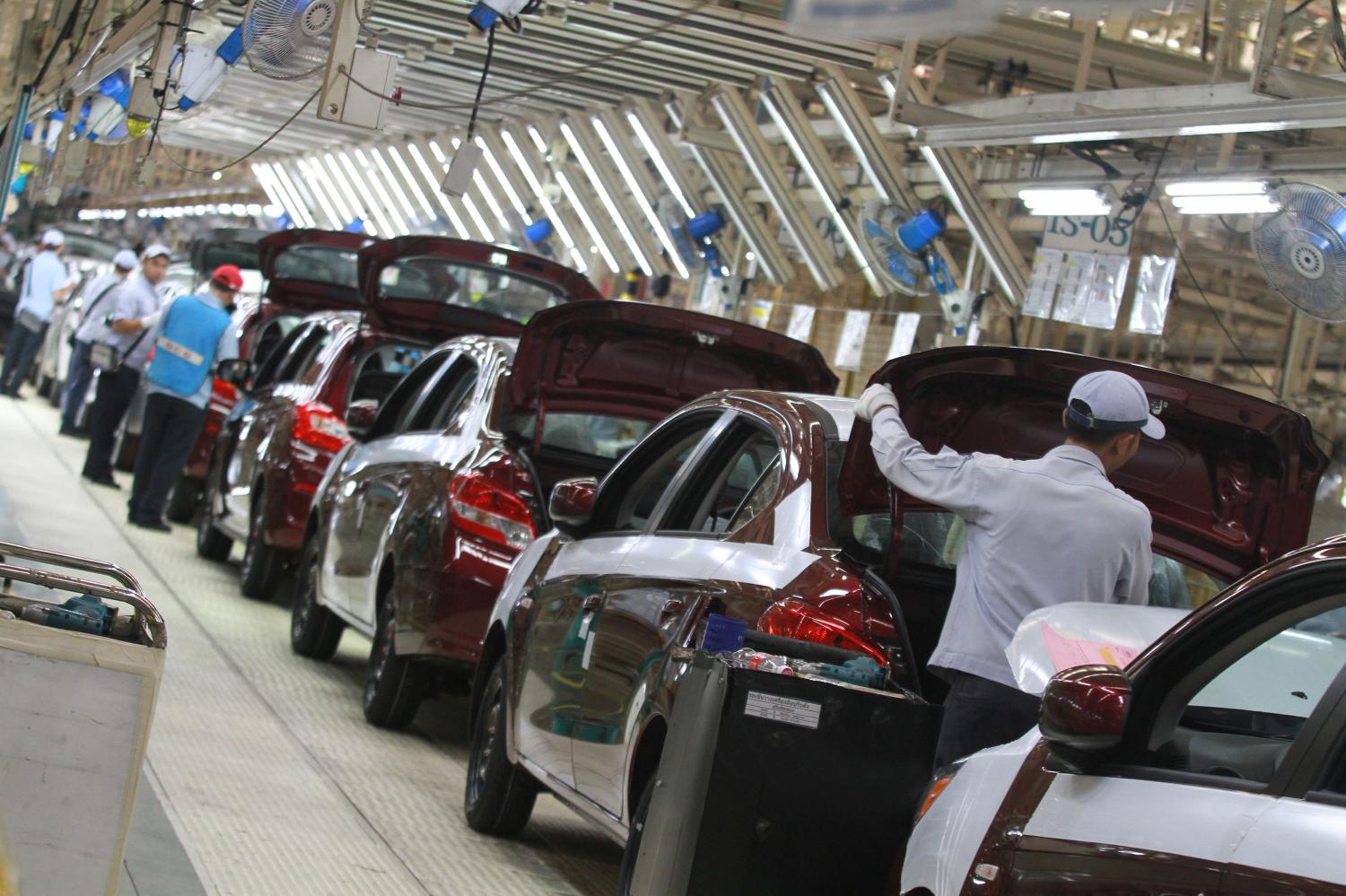
Workers inspect saloons on a production line at a manufacturing plant in Chon Buri province. Somchai Poomlard
CHINESE INFLUENCE
According to media reports, Tan Chong Subaru Automotive Thailand, a joint venture between Hong Kong-listed Tan Chong International Ltd and Subaru Corporation, announced on May 29 the closure of its factory in Bangkok's Lat Krabang district by the end of this year amid a market shift towards EVs in Thailand and the company's lacklustre sales performance.
This situation is similar to other markets around the world, said an automotive executive from the FTI who requested anonymity.
"Every market has seen an influx of Chinese-made cars, especially EVs, as the mainland market can't absorb the total output, prompting Chinese automakers to ship them out, with Beijing providing support," said the executive.
Chinese automakers also reported a decline in sales, with BYD the lone exception.
The US and EU have imposed measures to curb the entry of car imports, especially EVs from China, said the executive.
"But the situation in Thailand is worse than those developed markets as the economy is floundering and political uncertainties are emerging, which both hurt consumer confidence," said the FTI executive.
Chinese manufacturers with production facilities in Thailand have a very low ratio of locally produced parts as Thai and even Japanese suppliers cannot compete against Chinese suppliers in terms of cost, said the executive.
"We cannot compete because Chinese parts producers have a much bigger production volume through economy of scale. Mainland China has a large availability of natural resources domestically, while Thailand has to import raw materials, even steel, to serve domestic production," said the executive.
To stay afloat, major manufacturers such as Toyota Motor Thailand are focused on how to improve production efficiency and control costs. Some manufacturing staff have been allocated to serve other functions within the company, said the executive.
"Companies with hybrid EV production seem to have competitive advantages for the time being. Those without hybrid cars are in a more serious situation," said the executive.
Prime Minister Srettha Thavisin said earlier the administration would push ahead with plans to grow the EV industry, while also helping businesses linked to the production of ICE-powered vehicles, such as auto parts, as they played a key role in strengthening the country's automotive industry.
Yet the current downturn in car sales and limited resources available to develop the EV industry hamper that ambition.
Thailand recently lost its No.1 ranking for auto exports in Southeast Asia for the first time, said Kriengkrai Thiennukul, chairman of the FTI.
This, coupled with sluggish domestic car sales, has raised concerns Malaysia may overtake it as the regional automotive leader, he said.
The scarcity of skilled personnel in electric mobility technology may impede the expansion of the country's EV industry, said Mr Kriengkrai.
The Electric Vehicle Association of Thailand (EVAT) warned the country faces a critical shortage of EV specialists and skilled workers needed to fuel the growth of EVs and related industries, which last year struggled to fill several thousand professional and employee vacancies.
Most of the positions required candidates who graduated from a vocational school, while the remainder required applicants possessing a bachelor's, master's or doctorate degree.
The EV industry desperately needs experts in the fields of software, material science, simulation and user experience, according to EVAT.
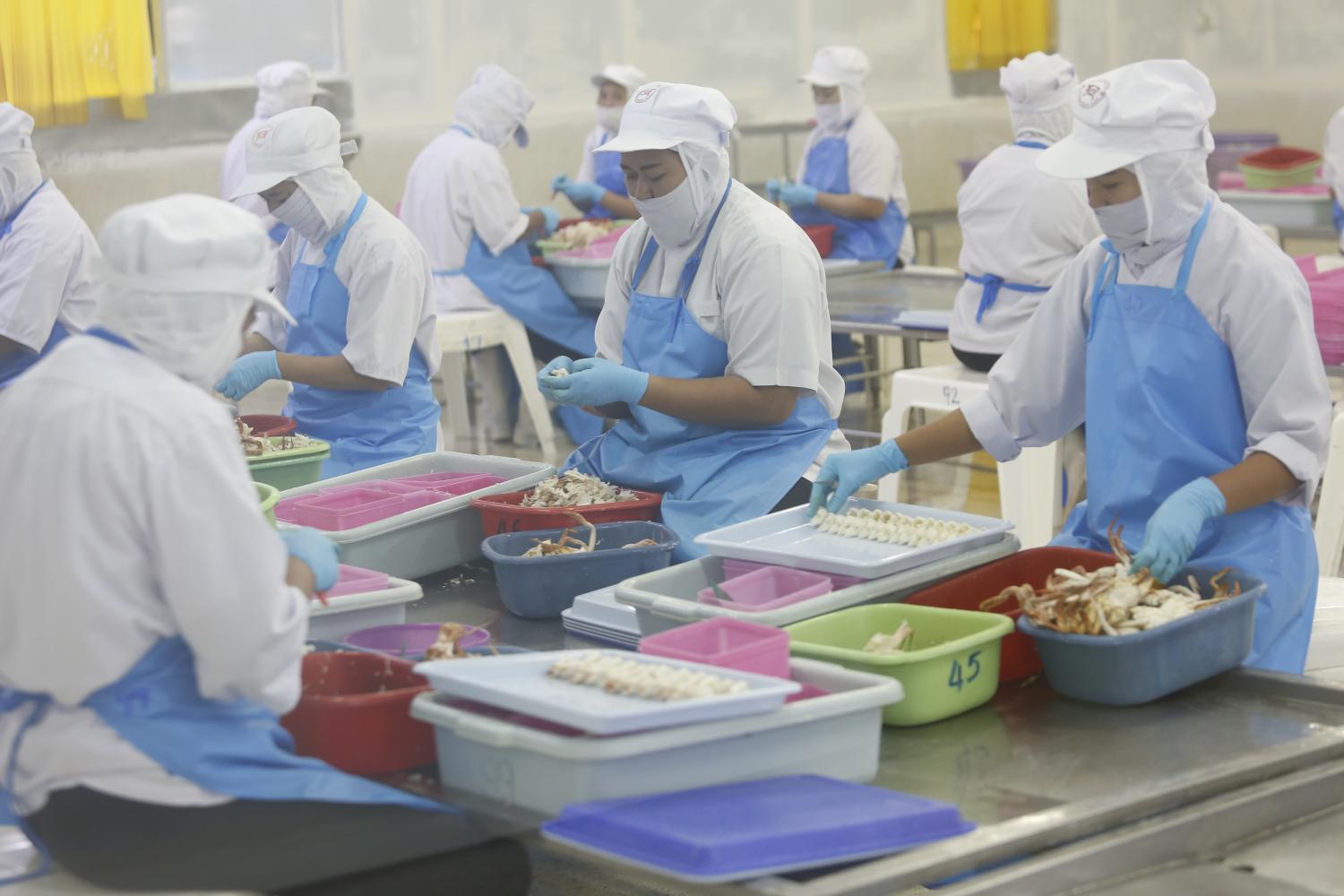
Workers at an assembly line process crab meat for export and domestic consumption. Pattarapong Chatpattarasill
TOUGH JOB
Nonarit Bisonyabut, an economist at the Thailand Development Research Institute, said a large number of Thai workers are still engaged in producing old world goods, instead of meeting the demands of the new world.
He said the problem lies in the slow development of Thai workers' skills to support the production of high-tech goods.
Although Thailand can keep up with important global trends, it still lags behind many other countries, resulting in a continuous decline in the country's GDP, said Mr Nonarit.
In 2019, prior to the pandemic, Thailand's GDP growth was 2.2%, according to the National Economic and Social Development Council (NESDC). In 2020, GDP contracted by 6.2%, then grew 1.6% in 2021 and 2.5% in 2022. Growth decelerated to 1.9% last year and this year is expected to post 2.5%.
"If we want our economy to grow, we must be able to produce goods that meet the needs of everyone in the world," he said.
Thailand has positioned itself as a contract manufacturer, or a smart production factory for the world, without having its own brand. This is not necessarily wrong, said Mr Nonarit.
For example, Taiwan, a technology exporter, particularly of chips that are at the heart of modern industry, is also a contract manufacturer for various brands.
Several countries such as Malaysia and Vietnam are trying to develop their own brands, including in the automotive sector, but so far have not succeeded, he said.
Mr Nonarit recommended the government urgently strategise and integrate educational institutions to produce personnel with the necessary skills, while working to attract investment in high-tech industries, which would increase the demand for skilled labour.
COLLABORATION IS KEY
Sampan Silapanad, president of the Electronic & Computer Employers' Association, said local electronics manufacturers are mostly foreign firms. The two major factors when choosing investment locations in Southeast Asia are cost competitiveness and availability of human resources, with the sustainability of water, electricity supplies and logistics networks minor considerations, he said.
"In terms of human resources, companies look at how they can have enough people to run the factories in a sustainable manner and possibly serve potential manufacturing expansion in the future," Mr Sampan told the Bangkok Post.
In terms of costs, Thailand faces intensifying competition as other countries not only offer investment incentives, but also grants, free land and, more recently, a global minimum tax (GMT), which is an internationally agreed-upon minimum rate of tax paid by large corporations.
The GMT allows companies to use tax rebates for activities such as R&D and sustainability, he said.
"Rich and clever countries usually draw investments from high-tech industries with those incentives. Thailand has comparatively less financial resources, so we might have to weigh what we can get in return if we offer such incentives to foreign investors. If we cannot compete, we have to switch to second-tier electronics manufacturing instead," said Mr Sampan.
The semiconductor industry faces a specific challenge. The US is wooing American companies to invest at home rather than overseas to avoid the impact of geopolitics, he said.
"Thailand remains competitive in the electronics industry, with up to 500,000 people employed directly. But to further strengthen competitiveness, we have to ensure foreign companies with manufacturing facilities here have transferred their knowledge to locals," said Mr Sampan.
"Otherwise, Thailand will have nothing much left if they leave after four or five years. Incentives are needed to stimulate knowledge transfer from foreign firms to Thailand through training and education.
"Local authorities must have constant conversations with companies to understand what the industry needs and the current obstacles they face, in order to collaborate to try and improve the situation."
RESEARCHERS REQUIRED
Thailand Science Research and Innovation (TSRI) said last week it allocated 8 billion baht for the country to bolster its supply of young researchers, aiming to support S-curve industries such as artificial intelligence (AI), EVs and quantum technologies.
The budget for fiscal 2025 also calls for equipping 100,000 employees to support the semiconductor industry, capitalising on opportunities stemming from geopolitical conflict.
In fiscal 2025, the government allocated a budget of 19.3 billion baht for R&D, covering 195 agencies and institutions. Of the total, 8 billion baht is for human development, with 2.5 billion of that amount to promote young researchers.
Nirawat Thammajak, vice-president of TSRI, said semiconductors represent a strategic industry in which Thailand needs to attract investment given the geopolitical tension between the US and China causing the relocation of plants away from Taiwan to Thailand, Malaysia and Vietnam.
Mr Nirawat said Thailand has the potential to provide 100,000 highly skilled workers to supply the semiconductor industry.
Thailand has 614,197 people employed in related industries, of which 130,757 are employed in semiconductors and integrated circuits, along with 483,440 in related industries such as computer manufacturing.
The Higher Education, Science, Research and Innovation Ministry is expected to propose to the cabinet the development of a workforce plan to fulfil future demand in the semiconductor industry, he said.
According to a Statista Market forecast, the semiconductor market in Thailand is projected to grow by 8.88% from 2024-2027, resulting in a volume of US$13.2 billion in 2027.
TRANSITION ASSISTANCE
The state strategy to cultivate new industries for the digital era should be complemented by support for businesses accustomed to traditional technologies and those that are becoming obsolete, according to the FTI.
"The development of S-curve industries is a gradual process, during which old industries must strive to adapt to changes to ensure their survival," said Mr Kriengkrai. "We are most worried about small and medium-sized enterprises prone to the negative impact of economic shifts."
He urged the government to develop new measures to help these businesses during the shift to modern industry. Without timely solutions, more factories could shutter as the economy plods along, said Mr Kriengkrai.
Thailand's Manufacturing Production Index fell by 5.13% year-on-year in March, declining for 18 consecutive months because of lower car manufacturing as domestic sales plunged, according to the Office of Industrial Economics. During the first quarter this year, capacity utilisation was only 60.4%.
The government's decision to impose a 7% value-added tax (VAT) on imported goods could slow the influx of cheap goods into Thailand, but it will not solve the problem, he said. Imported goods sold for less than 1,500 baht per parcel were previously exempt from VAT.
"If low-cost Chinese products continue to flood the Thai market, the manufacturing sector will bear the brunt," said Mr Kriengkrai.
Many local entrepreneurs already cut operating costs and use technology to enhance their factory production, but these measures alone are inadequate, as further government assistance is needed, he said.
Suchit Leesa-nguansuk