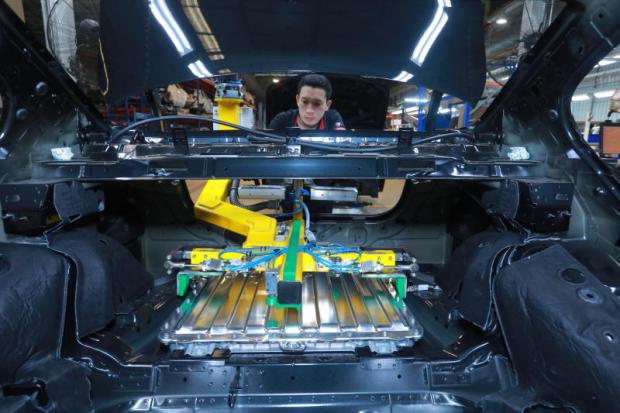
The Internet of Things (IoT) being built into product design, more service-centred business models, and 3D printing delivering major benefits have emerged as game-changing trends for manufacturing this year, according to IFS, a multinational enterprise software solutions specialist. The following article examines the three trends in detail.
1. By the end of 2018, more than 50% of manufacturers will be building IoT technology into the design phase of their products
"If we think of IoT as a product's nervous system, it is now growing from picking up signals at the periphery to being the brain of the product, constantly sending, receiving and gathering information throughout the product's lifetime, enabling new services and revenue streams," says Antony Bourne, global industry director of industrial and high-tech manufacturing at IFS.
According to Global Market Insights, IoT in manufacturing was valued at US$20 billion in 2016, with a compound annual growth rate (CAGR) forecast at 20% 2017-24. Current IoT investments are taking place in three main areas:
smart manufacturing to increase output, product quality or operations and workforce safety as well as reduce resource consumption;
connected products to enhance performance, including collecting detailed information on products in the field, remote diagnostics and maintenance;
connected supply chains to increase visibility and coordination, tracking assets or inventory for more efficient execution.
By engineering IoT technology into products and equipment already in the design process, manufacturers can monitor not only equipment performance to predict when it needs repair, but also how and when it is being used, which provides competitive advantages.
By the end of 2018 more than 50% of manufacturers will be building IoT technology into products from day one -- asking themselves what services and revenue the product can generate throughout its lifetime. That leads to the next key prediction:
2. Servitisation speeds ahead: By 2020 most manufacturers will earn more than half of their revenue from services.
With manufacturing becoming more commoditised, the need for businesses to differentiate themselves is a key to survival and profitability. Consequently, many manufacturers are shifting to a more service-centred model.
"Servitisation", as it's known, is a way for a manufacturer to add capabilities to enhance its overall offering in addition to the product itself. One famous example is Apple, which introduced iTunes to increase loyalty to its iPod and generate more revenue.
The benefits of servitisation can be found in what at first appear to be unlikely places. For example, Philips provides Schiphol airport in Amsterdam with "lighting as a service", which means that Schiphol pays for the light it uses, while Philips remains the owner of all fixtures. Philips and its partner Cofely are jointly responsible for the performance and durability of the system, and ultimately its re-use and end-of-life recycling. This has resulted in a 50% reduction in electricity consumption without having to buy a lamp.
For the global furniture manufacturer Nowy Styl Group, servitisation has been crucial to growth. In 2007, it announced "for us, chairs are not enough", starting a transformation from pure manufacturer to world-class office interior consulting company.
Another example is a cleaning product manufacturer that offers delivery and service-dosing systems. It understood that choosing the right cleaning products was just part of its customers' main goal. Applying the products in the most effective way, choosing the right accessories, establishing the right routines -- all these too were crucial to keeping premises clean.
The fact is, no matter how beautifully designed a chair is, or how effective a cleaning product is, today's luxury products can quickly turn into tomorrow's commodities, pulling prices down with them. With servitisation, manufacturers escape the corrosion of commodification. Expert services built on years of experience provide the kind of value customers will always pay for.
However, according to the IFS Digital Change Survey, almost one in three manufacturing companies have yet to derive value from servitisation. They are missing out on revenue streams and new ways to develop their offerings.
New technology such as IoT adds an additional layer to servitisation. With sensors detecting when your product or equipment needs service, this data can trigger an automated response that will make your service organisation more effective.
3. 3D printing is no longer hype: 3D printing, just like IoT, is entering a more mature phase. "No matter how big the 'wow' factor is when we first see it, apart from smaller-scale manufacturing production such as hearing aids and jewellery, 3D printing has so far failed to live up to its full potential. All this could change in 2018," says Mr Bourne.
Improved scalability is one major reason. 3D printing companies are moving into manufacturing traditionally dominated by injection-moulding specialists, with new, faster and better-connected automated systems that reduce some of the time-consuming pre- and post-processing that has been an obstacle to wide-scale adoption.
One such company, Stratasys, offers a new system called the Demonstrator, which combines three printers into a stack system -- each can communicate with its neighbours in real time. It is highly scalable, capable of printing from 1,500 to 2,000 components a day. Such economies of scale bring costs down, which will be an important catalyst for success.
The aviation industry is pioneering 3D printing technology, and the manufacturing industry can learn from that. One successful example is the new GE turboprop ATP engine, which was 35% 3D-printed, taking it down from 855 components to 12. The engine is now lighter and more compact, delivering a 15% lower fuel burn and 10% higher cruising power compared with rivals' offerings.
The expanded capacity and reduction in pre- and post-processing that innovative 3D printing companies offer will give manufacturers in other fields a similar ability to fly higher.
Antony Bourne is the global industry director of high-tech and industrial manufacturing at IFS.