When Schle Woodthanan, managing director of Textile Gallery, was a young journalist, he visited many factories, including his family-owned factory, and discovered that the working environments were poor. The bad conditions had a negative effect on the health of workers, so when Schle took over his family business, he decided to build a new green factory, Pasaya, manufacturing home textile products.
The Pasaya factory provided a better working environment and did not cause any pollution. In 1995, before any buildings were built at the would-be factory site in Ratchaburi, a wastewater treatment pond was first constructed.
"At that time, many factories caused water pollution because investors thought that wastewater treatment was a big expense that they could not afford. I thought differently because my first concern was the environment. At Pasaya, a wastewater treatment pond was built before the textile dyeing building. Our factory has never dumped contaminated water," said Schle.
With his far-reaching vision, Schle planned ahead to help mitigate climate change. The founder of Pasaya intends to make the factory a net zero emissions plant by 2050.
"The effects of climate change have become more severe, and factories can help by reducing carbon dioxide emissions. Many manufacturers do not want to reduce greenhouse gas emissions because they think the cost is high. But manufacturers can take loans from banks with low interest and/or they can ask state agencies for financial support. This kind of investment has long-term benefits. Pasaya invested in solar cells as clean energy and solar power paid back its expense in only five years," Schle explained.
In order to achieve net zero emissions, besides using solar panels, Pasaya replaced coal with liquefied petroleum gas for heating fuel in the dyeing and finishing process. LPG is more efficient than coal with its calorific value and emits less carbon dioxide. This will cut more than 2,500 tonnes of carbon dioxide emissions per year.
Growing trees is another practice that can help reduce greenhouse gas emissions. Instead of growing a few trees, Schle plans to grow a forest which will cover 100 rai of the factory in 2025. People at Pasaya estimate that the forest will be able to soak up 300 tonnes of carbon dioxide per year.
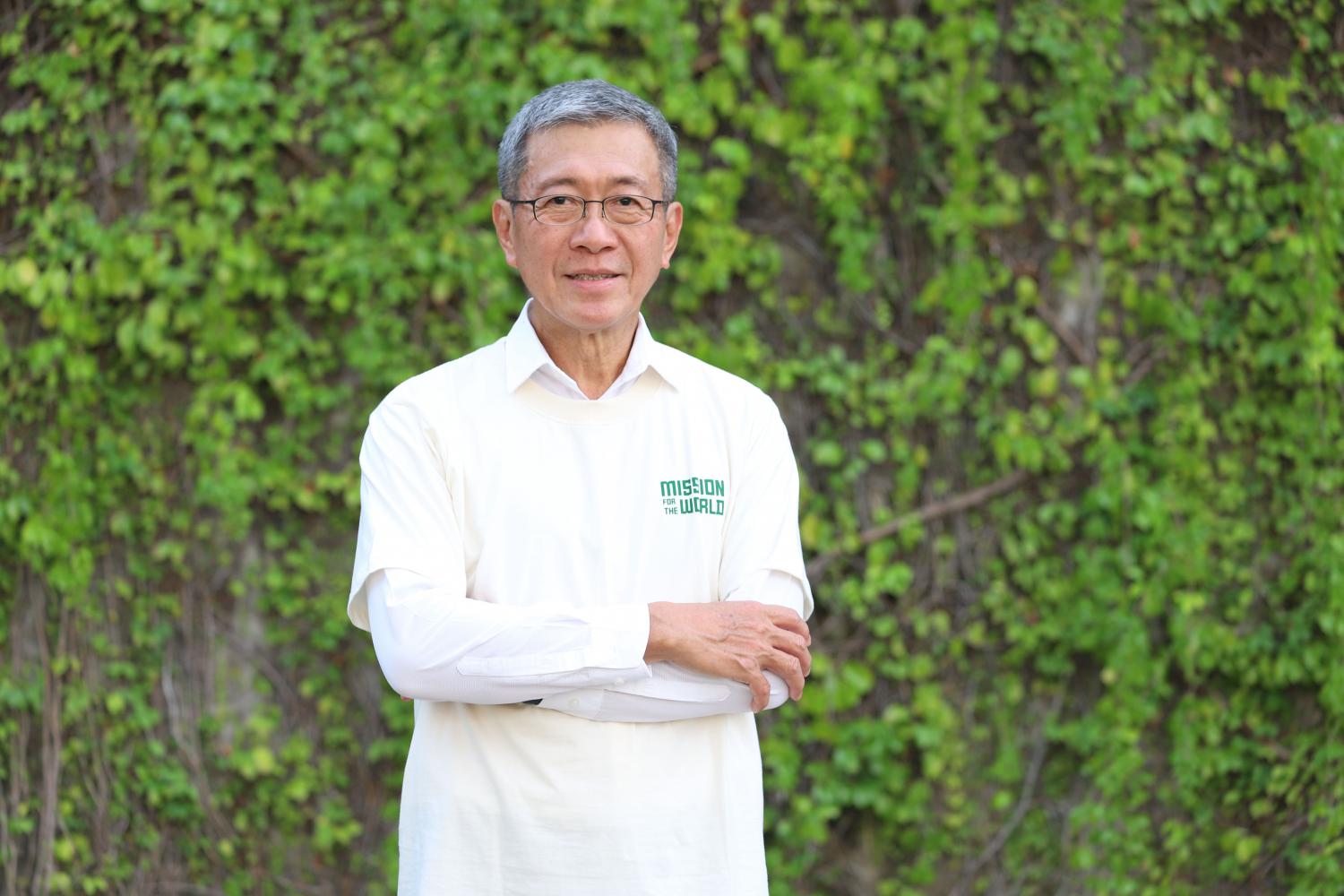
Schle Woodthanan, managing director of Textile Gallery. (Photo: Varuth Hirunyatheb)
"Although we had a coconut orchard in the Pasaya factory before, as city people, we do not know much about growing a forest. Since we aim to have 40 to 50m-tall trees, we consulted with Seub Nakhasathien Foundation and the Royal Forest Department about the best approach to take. Seub Nakhasathien Foundation also gave us Thai plants appropriate for the area such as yang na, ironwood and makha wood," said Schle.
Due to its environmental practices, Pasaya received a green industry label from the Ministry of Industry for its waste management.
"Pasaya's trash management has been a factory policy for over 20 years. In the early years, employees disposed of trash by burning it but that caused an unpleasant smell and produced carbon dioxide. I thought it was an improper waste disposal method, but people at that time were not aware of carbon dioxide emissions. I decided to dispose of the factory's trash by dedicating a landfill at the back not connected to or located close to any water resources. All garbage was buried in the landfill. After 20 years, the landfill covers 20 rai of the factory," Schle said.
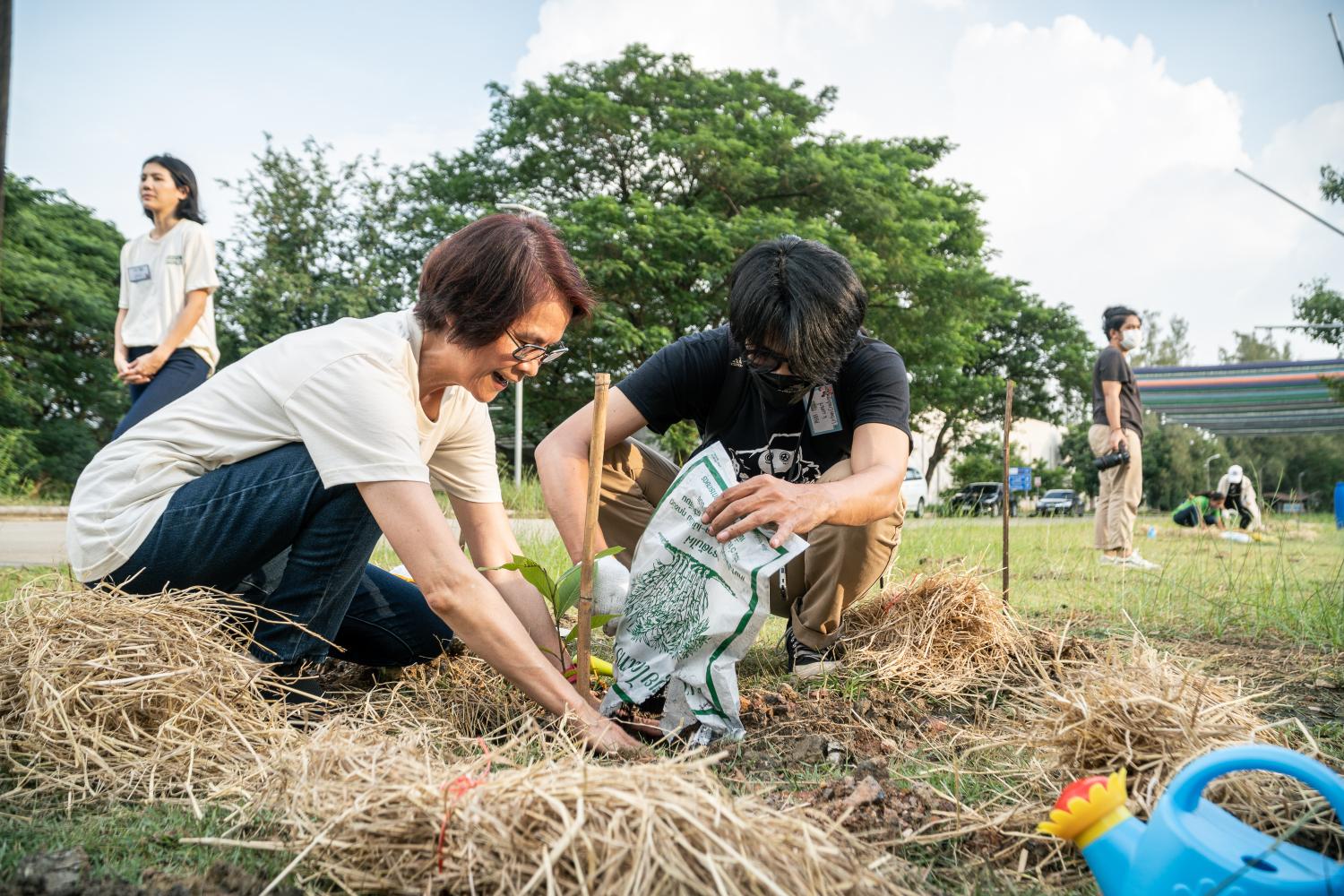
Pasaya plans to grow a forest which will cover 100 rai of the factory in 2025. (Photo courtesy of Pasaya)
Since 2018, Pasaya has also teamed up with PTT Global Chemical to upcycle polyethylene terephthalate (PET) bottles to produce new products. Schle confessed that at the beginning of the project, he was not sure if fibres from PET bottles would have a similar quality to natural fabrics but after running some tests, the results were positive.
"We decided to team up with PTT Global Chemical after we discovered that fabrics from PET bottles were just as tough and durable as natural fabrics. Since it was an upcycling project, we did not want to produce products that would be thrown away in a couple of years like clothes. Most people throw away their clothes after two or three years. We decided to turn PET fibres into carpets, wall fabrics and textile murals. Customers can bring us photos or family photos to create textile murals which can be used as wallpaper and last more than a decade," he said.
At Pasaya, there is an innovation department to create environmental products. One of Pasaya's outstanding innovations is energy-saving curtains.
"Many people think that curtains can prevent sunlight from entering a room and make the room cooler which can save electricity. In fact, curtains absorb heat and cause a room to have a higher temperature, but people who turn on the air conditioner do not feel it. Pasaya's energy-saving curtains use reflective electro-magnets which help reduce the temperature by 2C. With the lower temperature, the curtains help reduce the electric bill," said Schle.
Many factory executives may think it is impossible to achieve net zero emissions, but not at Pasaya. Schle affirmed that his goal to make Pasaya a net zero emissions factory by 2050 is possible.
"It is possible if everyone at Pasaya helps reduce carbon dioxide emissions as much as possible. I plan to install a second phase of solar cells at the end of 2023 or early 2024. For excess gas emissions, we can buy carbon credits from other developers. However, if Pasaya becomes the only net zero emissions factory in Thailand, it will not have much positive effect. I would like to encourage other manufacturers to take action to reduce carbon dioxide emissions. However, if customers continue to buy their products, they will not find it necessary to take action," he said.
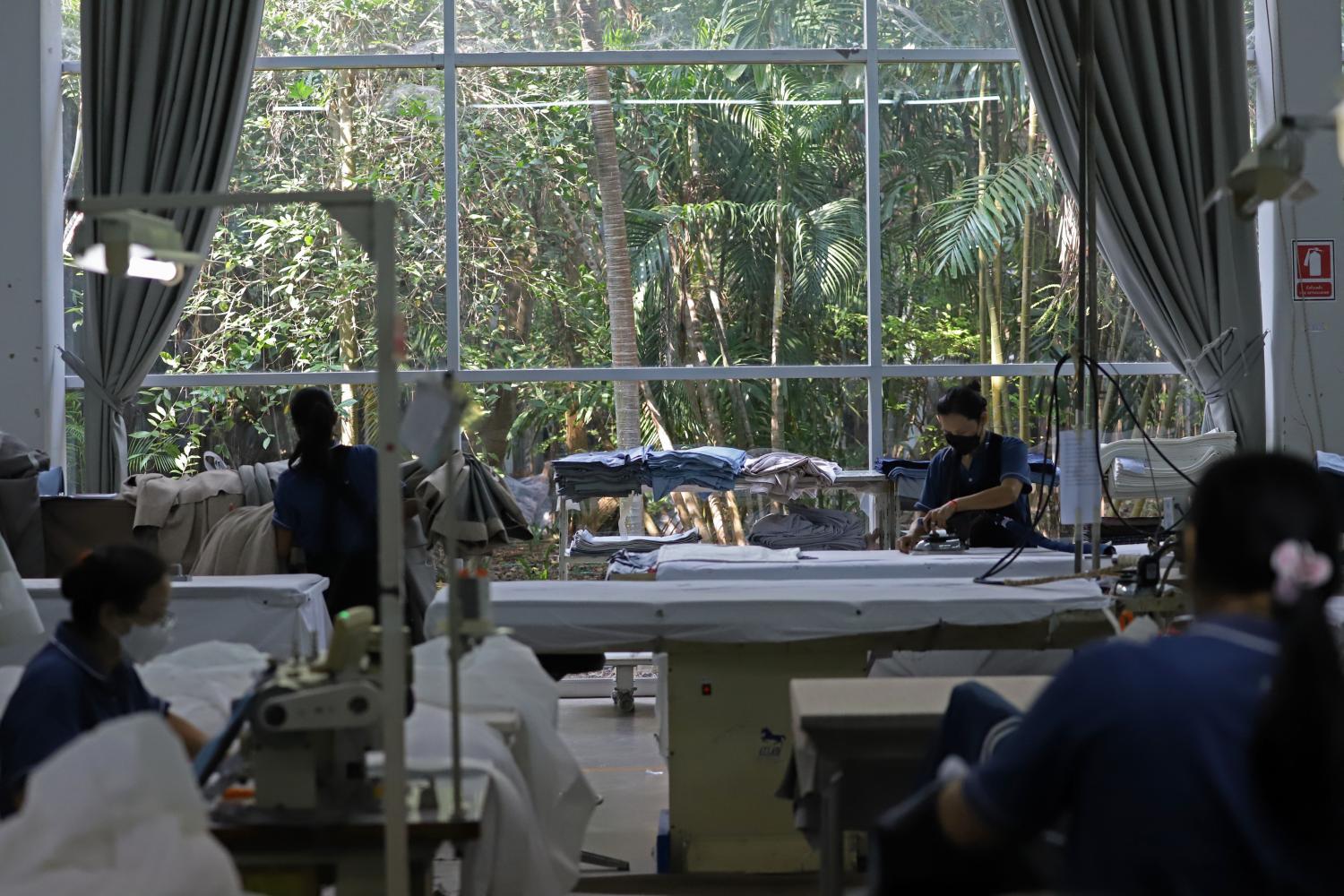
Employees in the sewing department sit next to a garden, for an improved working environment. (Photo: Varuth Hirunyatheb)
"I hope customers will choose to purchase products produced from factories registered as carbon footprint organisations with the Thailand Greenhouse Gas Management Organization [TGO] because these bodies have a limit of how much greenhouse gas is emitted and they allow TGO to track their carbon dioxide emissions. In the future, I believe there will be a label on products to inform consumers how much carbon dioxide is emitted in the production of an item and people can compare these numbers before making a purchase. If Thailand's manufacturers do not reduce the amount of carbon dioxide, we will face difficulty exporting our products to other countries."
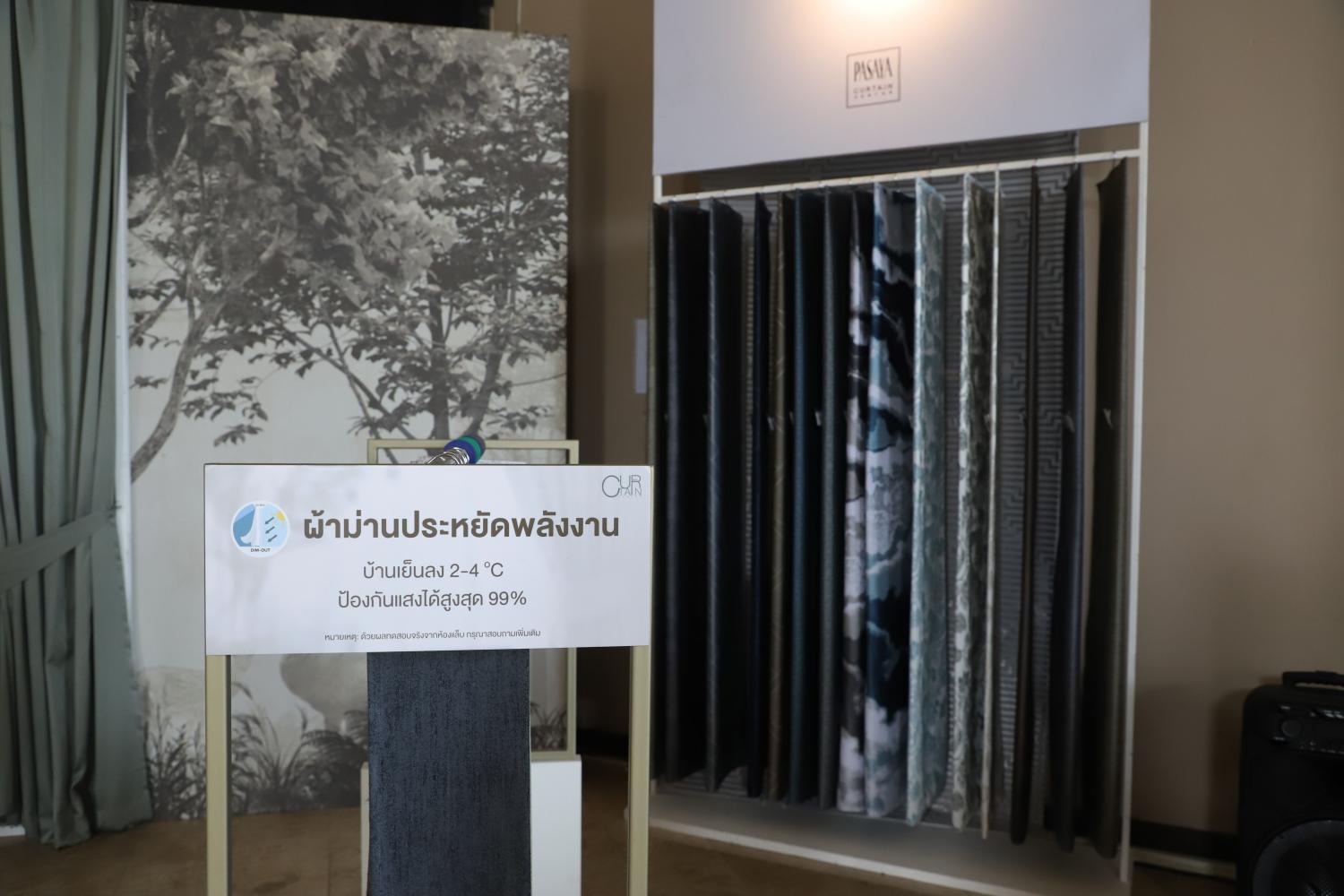
Energy saving curtains. (Photo: Varuth Hirunyatheb)
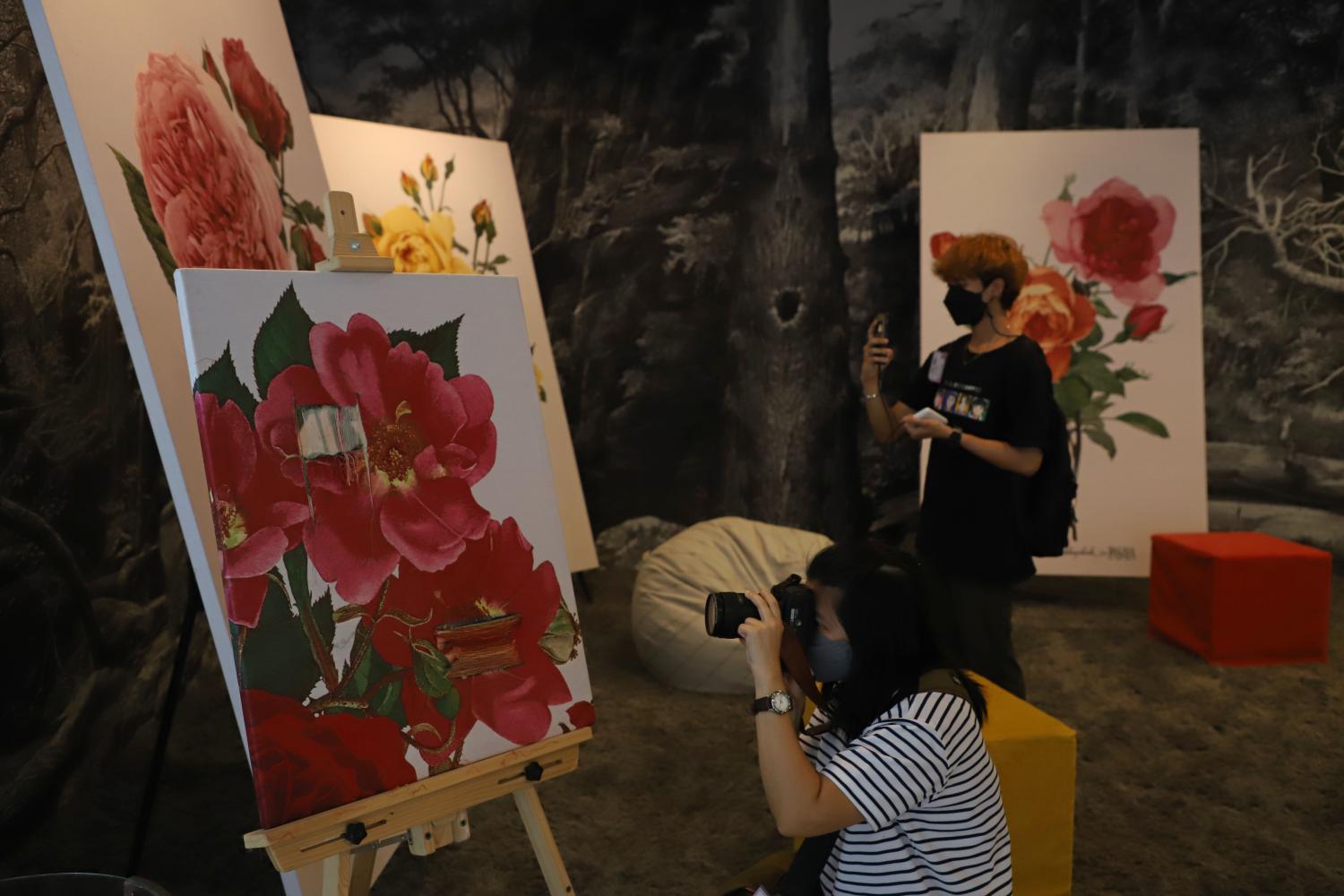
Textile murals. (Photo: Varuth Hirunyatheb)