Manufacturing, and more widely, industrial enterprises, are set to benefit the most from global digital transformation. The convergence of 5G, artificial intelligence (AI) and cloud computing have resulted in a multitude of use cases that address the biggest challenges facing industrial enterprises -- from difficulties with quality control, high machine maintenance costs, connection stability, data security, and rising labour costs. The time to transform is now.
Industrials made up 30% of Thailand's gross domestic product of about 16 trillion baht in 2020. Information technology spending accounts for 4% of GDP, with industrial enterprises estimated to be the top IT spenders in 2021 -- 20% higher than the finance sector and 80% higher than information and communication technology.
While the main thrust of this spending is to digitally transform traditional businesses and make optimum use of new cloud, big data and artificial intelligence applications, at the foundation is the need for agile, mission-critical infrastructure based largely on service level agreements.
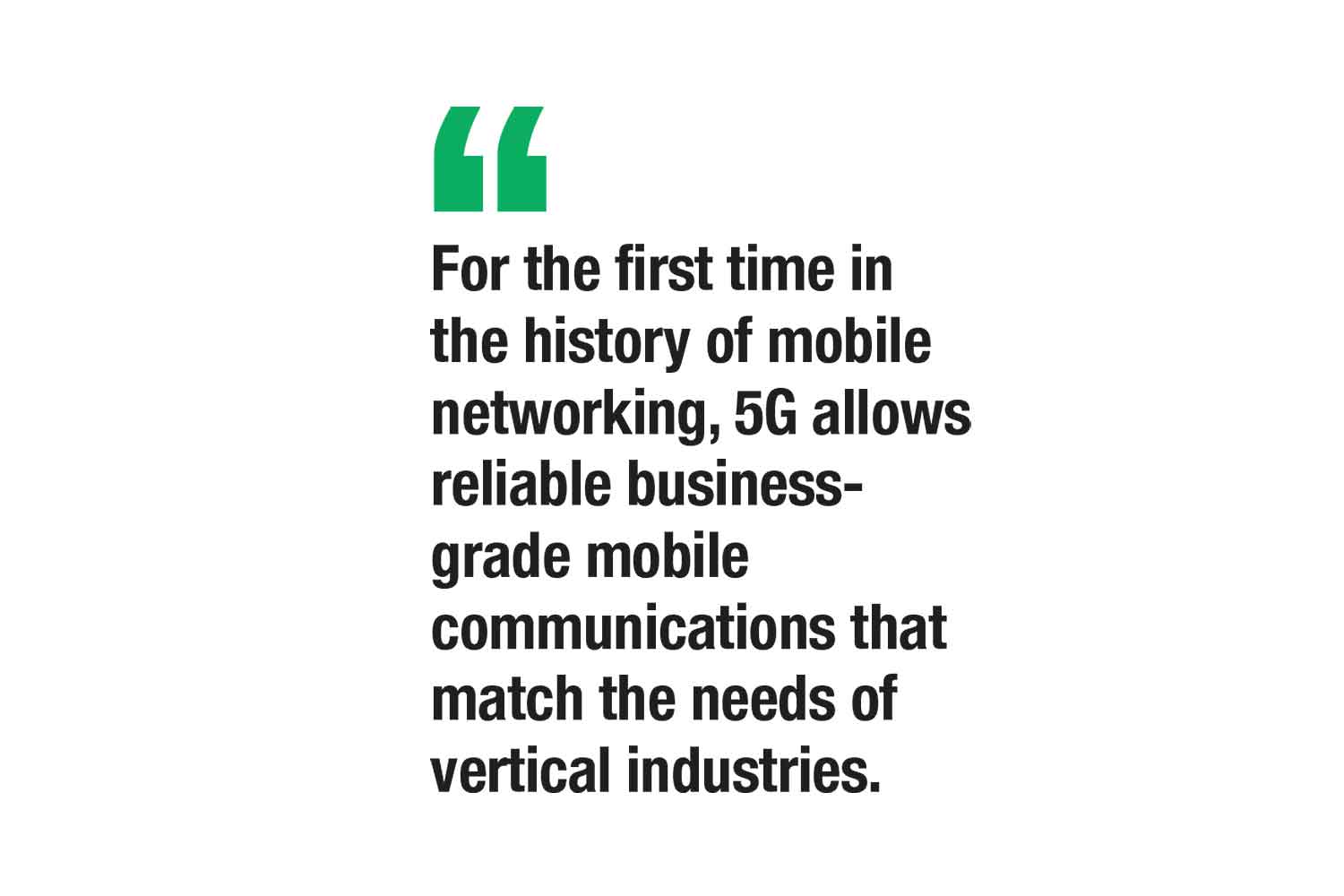
5G combines several critical elements including ultra-low latency for real-time control, massively scalable connectivity for the Internet of Things, network slicing for secure virtualised network segmentation, and mobile edge computing for improved responsiveness. And for the first time in the history of mobile networking, 5G allows reliable business-grade mobile communications that match the needs of vertical industries.
In China, 5G has been deployed in over 200 factories with measurable benefit in terms of performance and cost. Specifically at Midea, 5G replaced traditional WiFi for its automated guided vehicles for an 8% improvement in logistics efficiency and a 10% reduction in operation and maintenance cost due to increased connection stability.
At IKD, a leading supplier of automotive aluminium die castings used in 70% of all cars, 5G replaced over 10 kilometres of cables connecting 600 machines, reducing cable maintenance costs to near zero and increasing the product yield rate by 10%.
PRACTICAL USE CASES
While 5G manufacturing is still developing, the pain points are easily recognised as manufacturers in electronics, food and beverage production, automotive and more, look for ways to shake off the pandemic hangover, increase quality and productivity, and decrease costs. A 5G infrastructure provides the foundation for agile, reliable services and is a critical building block to unlock some exciting use cases for manufacturing. Let's look at four promising examples:
5G Robotics in production lines represents the largest value to manufacturers and can immediately be used to ensure production consistency and reduce labour costs. Industrial robots are mainly adopted in manufacturing factories with high demand, repetitive and high precision tasks such as automotive, food and electronics, aligning with three of the four largest manufacturing sectors in Thailand.
Using articulated arms programmed for industrial tasks such as welding, material handling, packaging and assembly lines, robotics requires stable high-bandwidth low-latency connectivity to enable flexibility and consistency of automation processes.
5G AR Industrial Maintenance uses cloud augmented reality technology for industrial maintenance, and utilises ultra high-resolution cameras to provide maintenance assistance from specialists in distant locations. With a lack of local specialists, difficulty attracting foreign specialists, and the high cost incurred from machine downtime, 5G AR industrial maintenance facilitates instant maintenance while allowing specialists to work in different locations.
The 5G Industrial Campus model provides fixed wireless access for private use and delivers ultra-reliable, high-speed and low-latency connectivity for smart manufacturing with various 5G applications. Notably used for industrial estates that provide network infrastructure for manufacturers, 5G Industrial Campus provides a single, converged, flexible and secure wireless infrastructure to meet the ever-changing requirements of manufacturers.
5G Remote Controlled Forklifts utilise 4K cameras and high-bandwidth connectivity for real-time teleoperation of forklifts from remote operations rooms. Used in warehouses to lift equipment or inventory in restricted environments, such as food cold storage and in hazardous areas, 5G remote-controlled forklifts connected provide improved safety and efficiency.
The above four common use cases can serve as a guiding light for focused adoption. In fact, a 2025 forecast shows these four use cases alone could produce as much as 1.4 billion baht in additional service revenue.
EEC FLAGSHIP
To further encourage 5G adoption and develop an active ecosystem in Thailand, Huawei has established the 5G Ecosystem Innovation Center (EIC) with the Digital Economy Promotion Agency (Depa). The facility works closely with Open Labs in China and around the world and benefits from use case and knowledge-sharing from global partners. Open to all, the 5G EIC already has over 70 partners and serves as an incubator for 5G innovation.
Resonating with Thailand's 4.0 strategy, which comprises Smart Industry, Smart City and Smart People, technology investment and support is necessary to achieve the fully transformed Thailand target in 2027 with Industry 4.0.
Looking at the Eastern Economic Corridor, potentially representing 40% of the country's GDP and the largest region for manufacturing, the local government and regulators should focus on 5G adoption and help transform the EEC into an advanced manufacturing hub for R&D and commercialisation of automation, robotics and smart systems.
The EEC is the perfect starting ground, led by electronics, food and beverage processing and automotives, to turbocharge manufacturing in Thailand, make optimum use of new ICT applications and usher in Industry 4.0 throughout the country.
Michael MacDonald is chief digital officer and executive consultant with Huawei Asia Pacific.