Sustainability has moved to the top of the global agenda—and the imperative to combat climate change is particularly urgent in Asia. The region could face more intense impacts than other regions, with its high volume of low-lying coastal cities exposed to flood and typhoon risk, sharp increases in heat and humidity anticipated across the region, and extreme precipitation or drought depending on the location.
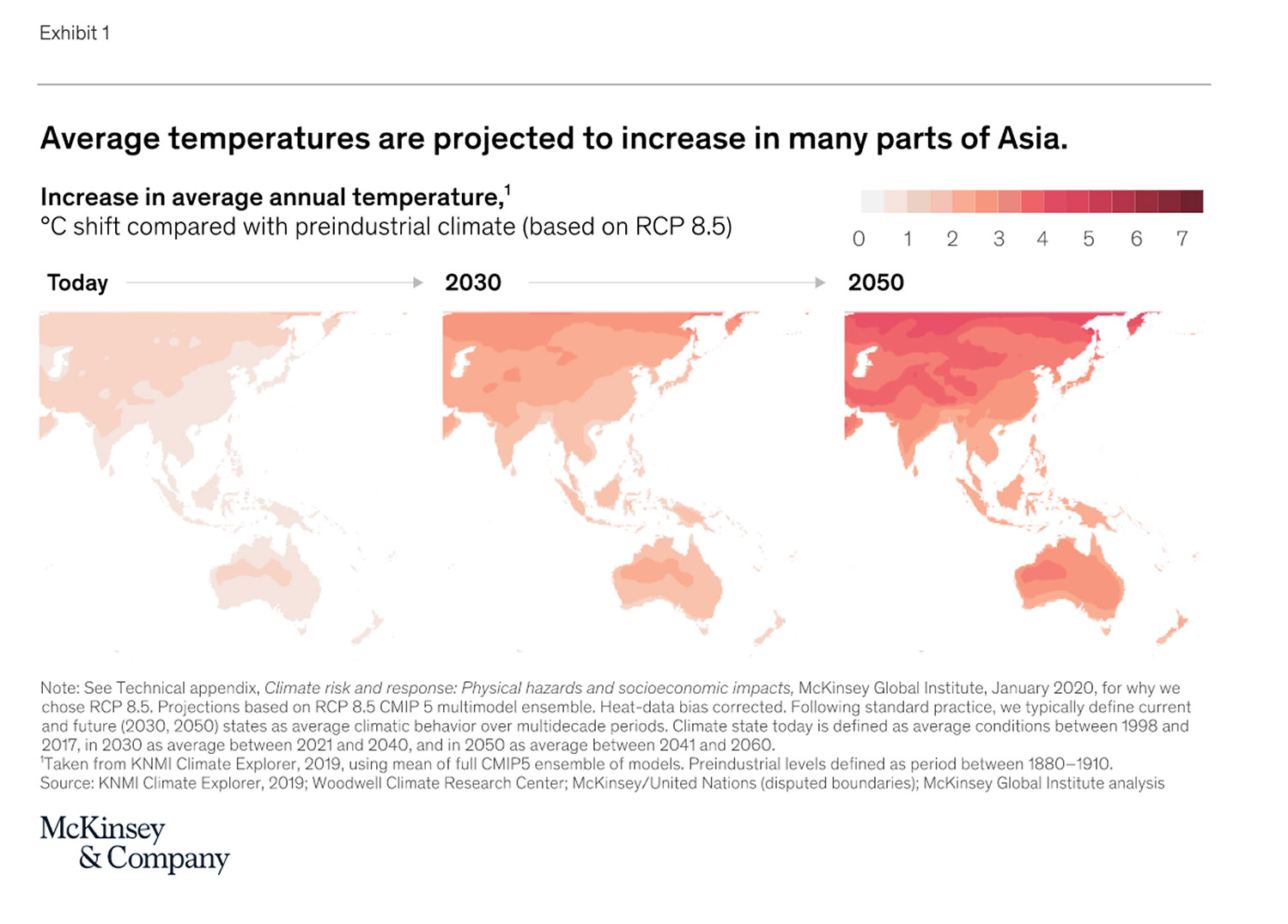
At the same time, significant shifts are happening in the world of work, primarily around the increasing role of digital technologies across every sector. Preparing the workforce for the future and making full use of innovative technologies will be crucial for securing long-term economic competitiveness. As Thailand seeks to boost the recovery of the manufacturing sector following COVID-driven disruptions, Fourth Industrial Revolution (4IR) technology adoption can play a critical role.
It is clear that sustainability and digitisation are key priorities for growth—but it is essential to recognise that these priorities are not at odds with each other. 4IR technologies can both boost productivity and smooth the transition to the future of work, while advancing environmental sustainability.
Sustainable digitisation in manufacturing
Take, for example, manufacturing. At present, some may believe that improving manufacturing productivity must come at the expense of environmental sustainability. If we are to meet the ambitious (but necessary) climate goals set by governments and policymakers across the globe, this assumption—that sustainability and productivity are at odds—must be challenged.
In light of a recent report from the Intergovernmental Panel on Climate Change (IPCC) described by the United Nations as “a code red for humanity,” more and more industrial companies across the world are challenging the assumption. And there’s no question that manufacturers face a progressively complex set of questions on sustainability.
For example, reducing energy costs through increased efficiency or on-site renewable-energy production is becoming a societal mandate in more and more markets. Yet even though the payback can be high for projects that do this successfully—both to the bottom line and to reduced environmental impact—significant barriers often hinder implementation at scale.
How can manufacturers achieve eco-efficiency, in accelerating their sustainability efforts without diminishing productivity—and in turn, competitiveness and profitability? The application of 4IR technologies on a broader scale may be the answer.
Applying 4IR technologies to enhance sustainability and productivity
The Global Lighthouse Network (GLN), a World Economic Forum initiative in collaboration with McKinsey & Company, is showing how 4IR technologies—think artificial intelligence, robotics, and IoT—build crucial digital capabilities. Collectively, GLN factories are transforming the manufacturing sector by showing how smart production can also be green.
The results speak for themselves: by deploying advanced technologies such as advanced analytics and artificial intelligence in the production chain, 64% of the 90 Lighthouse factories are already seeing the impact on environmental sustainability.
Almost 64% of Lighthouses report sustainability impact as part of their 4IR transformations—but some companies go above and beyond regarding sustainability, to the extent that sustainability is the foundational driving force of their business agendas. They are explicit about incorporating sustainability goals with specific timelines as part of their 4IR journey.
The new designation of “sustainability lighthouse” has been created to recognise these leaders. In addition to revolutionising manufacturing operations characteristic of other GLN sites, ‘sustainability lighthouses’ illustrate their commitment to environmental sustainability in novel and inspiring ways. Although there are no such Lighthouses in Asia yet, all GLN members—whether newly recognised or existing—could be designated sustainability lighthouses in the future.
A case study: Thailand’s first Lighthouse
Recently, Western Digital’s Pranchinburi site became Thailand’s first Lighthouse factory. In light of the rapidly growing demand for hard disk drive (HDD) products—along with the stringent quality requirements and rising cost pressure around such products—Western Digital Thailand turned to 4IR technologies to provide new solutions.
By leveraging connectivity and advanced analytics technologies, plant leaders were able to transform their capacity-saturated manufacturing site into a digital operation system with real-time visibility across suppliers, production, logistics, and customers. They also gained rapid access to real-time data-based insights, unlocking access to enhanced planning and predictions.
Ultimately, their 4IR transformation increased factory output by 123%, avoiding 30% in procurement and production costs and reducing product return rate by 43%.
Moreover, 4IR technologies also allowed the organisation to reduce GHG emissions while simultaneously cutting logistics costs. The company deployed an automated logistics system combining operational data with IoT and machine-learning tools to develop a shipment-consolidation-and-logistics optimiser. This tool allowed the organisation to reduce logistics costs by 47% and GHG emissions by 12%, largely by eliminating unnecessary shipments.
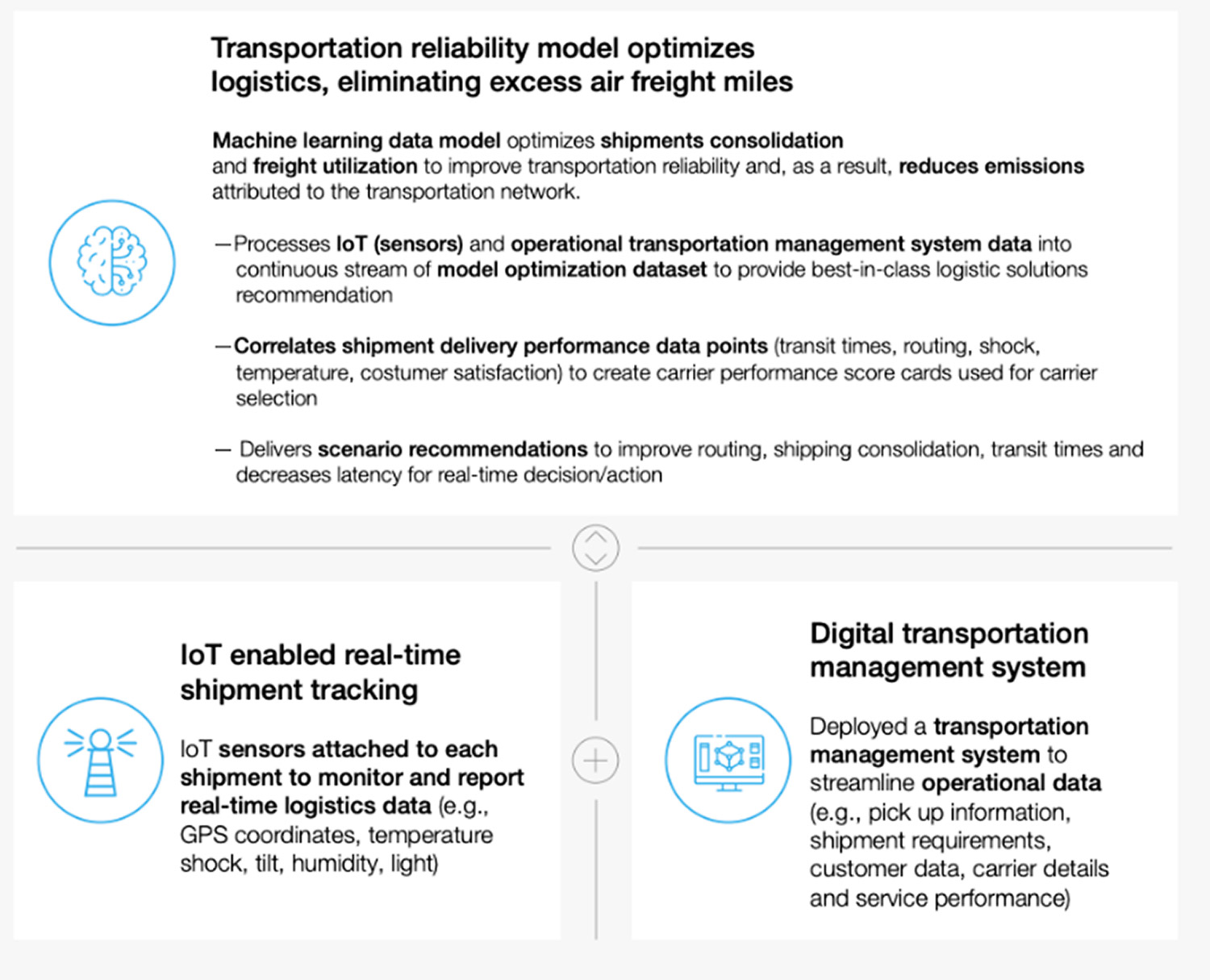
What’s next for Thailand?
According to the Office of Industrial Economics (OIE), just 25% of Thailand’s factories currently use robotics, automation, and systems integration. With the country aiming to become a robotics and automation hub in ASEAN by 2026, it’s clear that accelerating the use of 4IR tools and technologies will be critical.
The wider adoption of robotics in high-growth industries could boost the development of advanced manufacturing in Thailand. For example, the Ministry of Industry is preparing to help SMEs modernise their manufacturing operations by establishing a 2.5-billion-baht soft loan program to help upgrade factory technology to robotic and automation systems. The initiative builds on the government’s Thailand 4.0 plan, which envisions an economic transition supported by technological advances and high-level services.
As well as driving manufacturing efficiency—and in turn productivity and profitability—the acceleration of Industry 4.0 adoption in Thailand could also pay dividends for environmental sustainability. By embracing 4IR-driven transformation, a new kind of eco-efficiency becomes possible, where sustainability and competitive excellence are not only compatible, but interwoven.
The critical need for 4IR technology adoption in manufacturing
The pandemic has highlighted that manufacturing players ahead of the game in adopting 4IR technologies are better at navigating periods of unprecedented change. UNIDO and UN Thailand’s Impact Assessment of COVID-19 on Thai Industrial Sector revealed that it was “small-size and low-tech firms” that “suffered the most from the crisis,” with manufacturing taking the most severe hits across the sub-sectors of automotive, petroleum, and petroleum products, malts and malt beverage, air conditioning systems, and sugar. In contrast, companies that already have critical capabilities—such as manufacturing-execution systems, IT/OT stacks, and data marts or data lakes—in place are poised to speed ahead.
In a McKinsey survey of over 400 companies worldwide, 62% of the Southeast Asian respondents said that Industry 4.0 technologies played a critical role in their crisis response, with agility and customer-centricity coming out as the highest strategic priorities.
This goes to show how critical adopting 4IR-driven technologies across the manufacturing industry in Thailand will be for sector recovery from COVID-19. As noted in UNIDO and UN Thailand’s Impact Assessment, the pandemic is likely to accelerate the structural transformation of the manufacturing sector. With the right investments in place, the industry’s ‘next normal’ could be more resilient and sustainable.
About the Authors: Alpesh Patel is a partner in McKinsey & Company’s Singapore office, where he leads the firm’s Digital Capability Centers in Asia Pacific. Parimol Karnchanachari is a Partner based in McKinsey & Company’s Bangkok office and leader of the firm’s chemicals work in Southeast Asia. Further information contact Alan Laichareonsup at email: Alan_Laichareonsup@mckinsey.com
Series Editor: Christopher F. Bruton, Executive Director, Dataconsult Ltd, chris@dataconsult.co.th Dataconsult’s Thailand Regional Forum at Sasin provides seminars and extensive documentation to update business on future trends in Thailand and in the Mekong Region.